During my internship at Atlis Motor Vehicles I was tasked with evaluating the viability of a certain type of battery enclosure. To accomplish the goal of evaluating the enclosure I needed to make a small scale model to perform tests on. To make the model I decided to build a low cost thermoforming machine.
The main components of the thermoforming machine are the stand, vacuum system, plenum, and heater. I first did some research on the main components of the machine and then start working on a model in Solidworks and Fusion 360. Some of the requirements were that the machine needed to be oriented vertically, have a small footprint, and be operable by any employee. An early CAD concept can be seen below. Unfortunately most of the files were done using the employers CAD software so the final files are not available.
For the vacuum system an 11 gallon tank was used with a pump that was laying around the shop. A vacuum gauge was attached to the tank to determine if a sufficient vacuum was created to pull a part. A two valves were also used so that a vacuum could be pulled independent of pulling a part. The vacuum system was attached to the bottom of the plenum and was the first system tested. The next system was the heater. Overall the heater was the biggest challenge in the project. To make the heater I used nichrome wire and a power supply. Due to the hardware available the current did not flow through the wire evenly and hot spots formed.
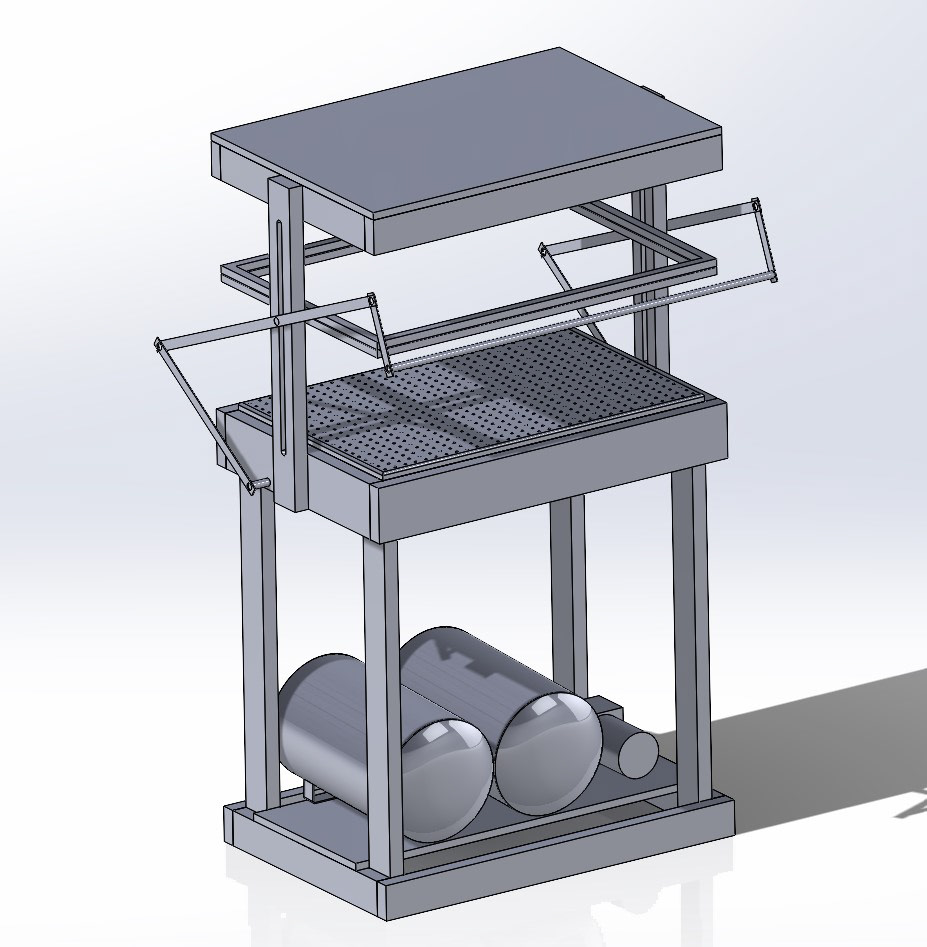
This issue was mainly caused by wires that were not equal lengths. Further optimization of the heater was needed to get sufficient heat to reach the forming temperature on the desired materials such as polycarbonate. As for the overall effectiveness of the machine the heater was the limiting factor. Only thin sheets of materials like ABS could reach sagging temperature using this heater. The desired materials could not be formed.
There are several improvements that could be made to the machine to improve the usability:
- Add a second vacuum tank
- Improve the heater
- Use a lighter frame to hold plastic sheet
The first improvement would be to use a second vacuum tank to increase the volume of air and thus "sucking power" the machine has. This would result in the material forming closer to the mold and more accurate parts. The second major improvement would be to improve the heater design or just purchase a COTS heater. The effort to wire and troubleshoot the heater ended up bottle-necking the whole project. Smaller improvements would be to lighten the sheet frame (not shown). The sheet frame was made of steel bar stock due to availability and was welded into a hollow rectangle. Holding the sheet for heating was fatiguing and aluminum could have been used. Adding a seal to the plenum would have also helped to improve the part accuracy.