My senior year at LMU I was approached by Prof. Hawkins to assist with the full CAD design of a convection fluid device. I was the sole engineer on the project and outside of a few requirements had the freedom to design most of the components from scratch. Below is an iso view of the design that I completed before handing it off to another student to integrate a new motor assembly.
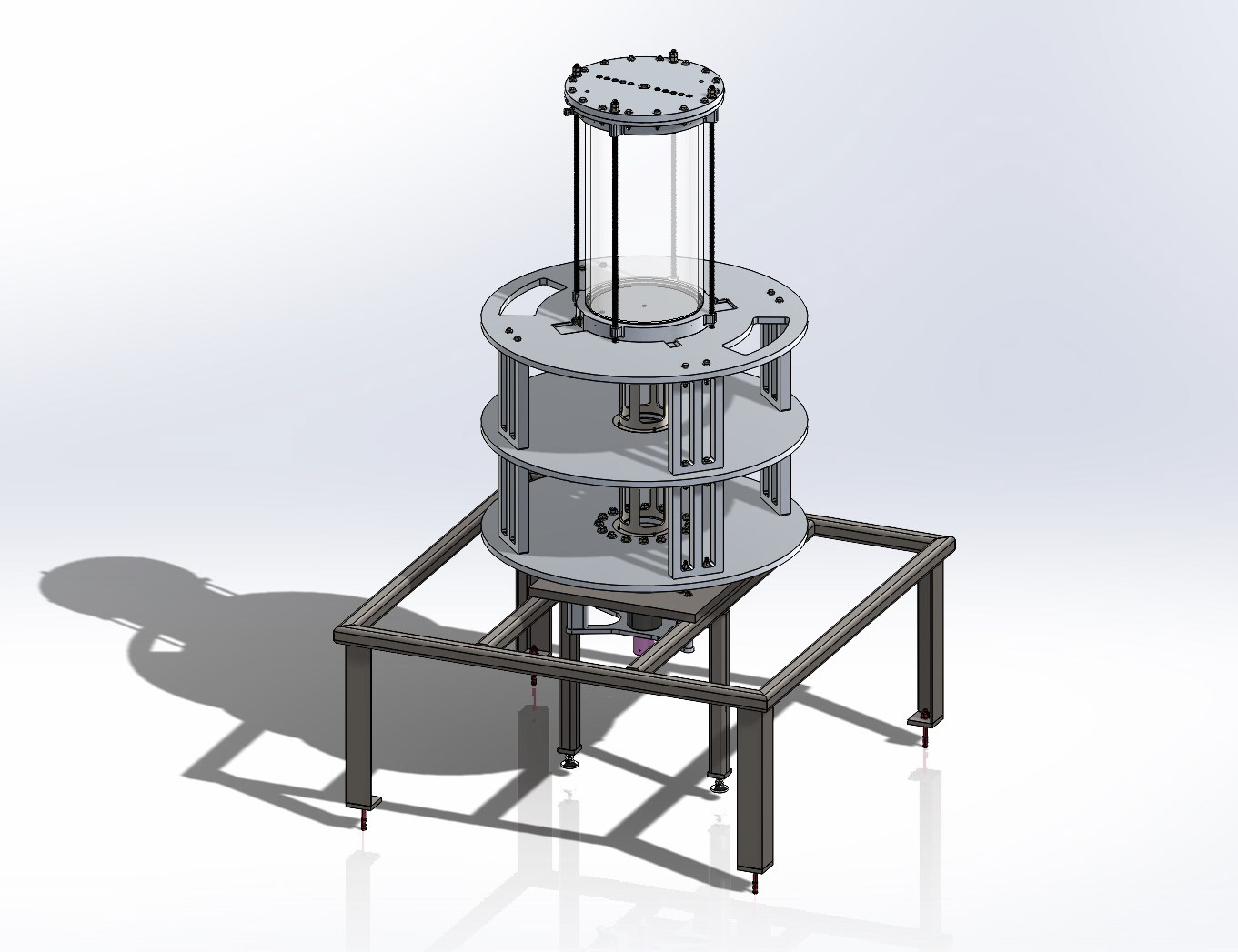
The device consists of a tank, heat exchanger, center table, and frame. Each of the sections are shown discussed more detail below. To begin the design on this project I received a list of key requirements such as tank volume and diameter, a sensor list, and a desired assembly order. From here I began to develop the tank section which was most critical to experiments that will be run on the machine. Some details of the tank assembly can be seen below including the heat exchanger.
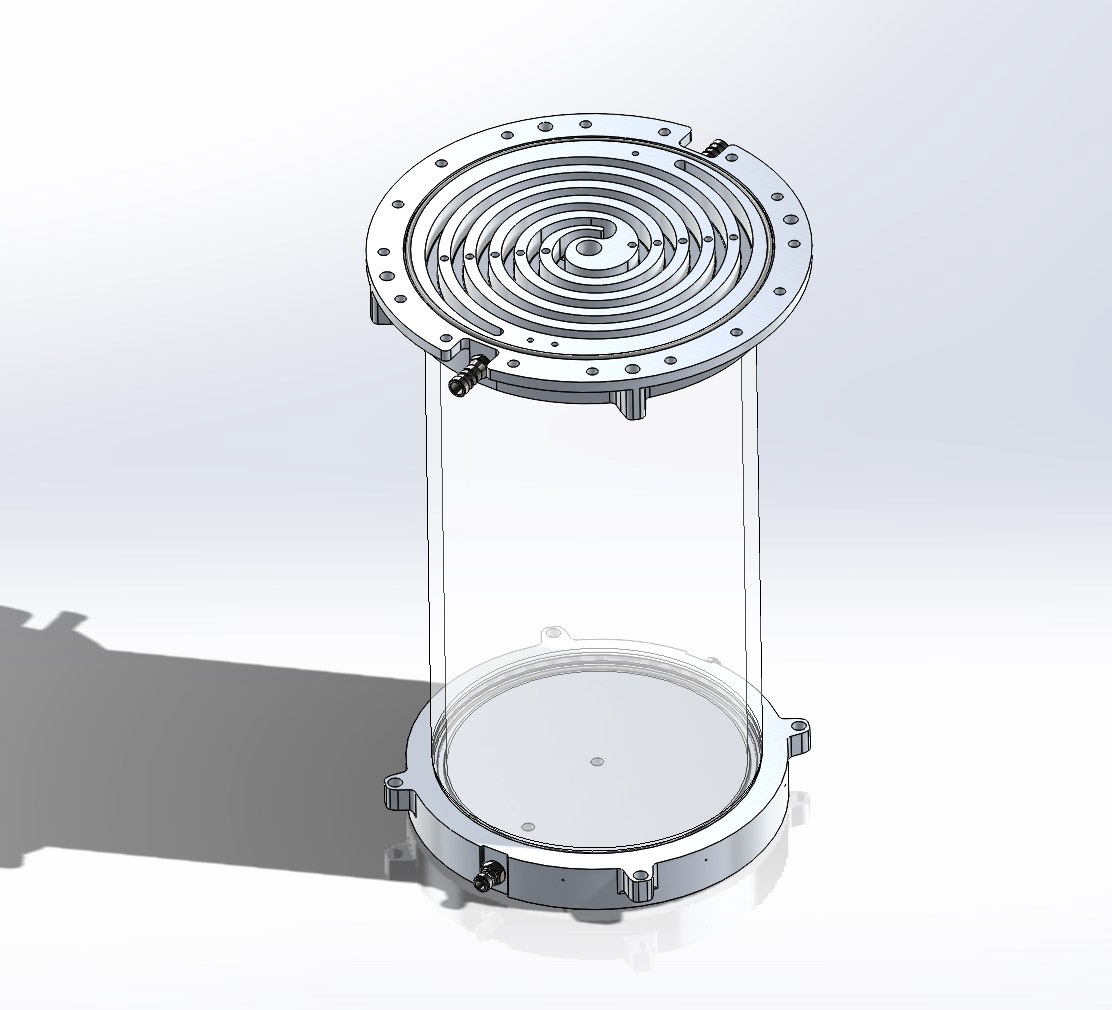
The tank lids were the most complex part of the entire assembly. Due to the double spiral heat exchanger the design was focussed on maximizing the area of the heat exchanger first and pressure drop second. This specific geometry was required by the professor due to its uniformity in cooling performance. Thermal and fluid simulations were run after the design was completed and will likely be revised by another student before production. The design for both lids also includes NPT fittings, plugs, sensor access, and the holes for bolting.
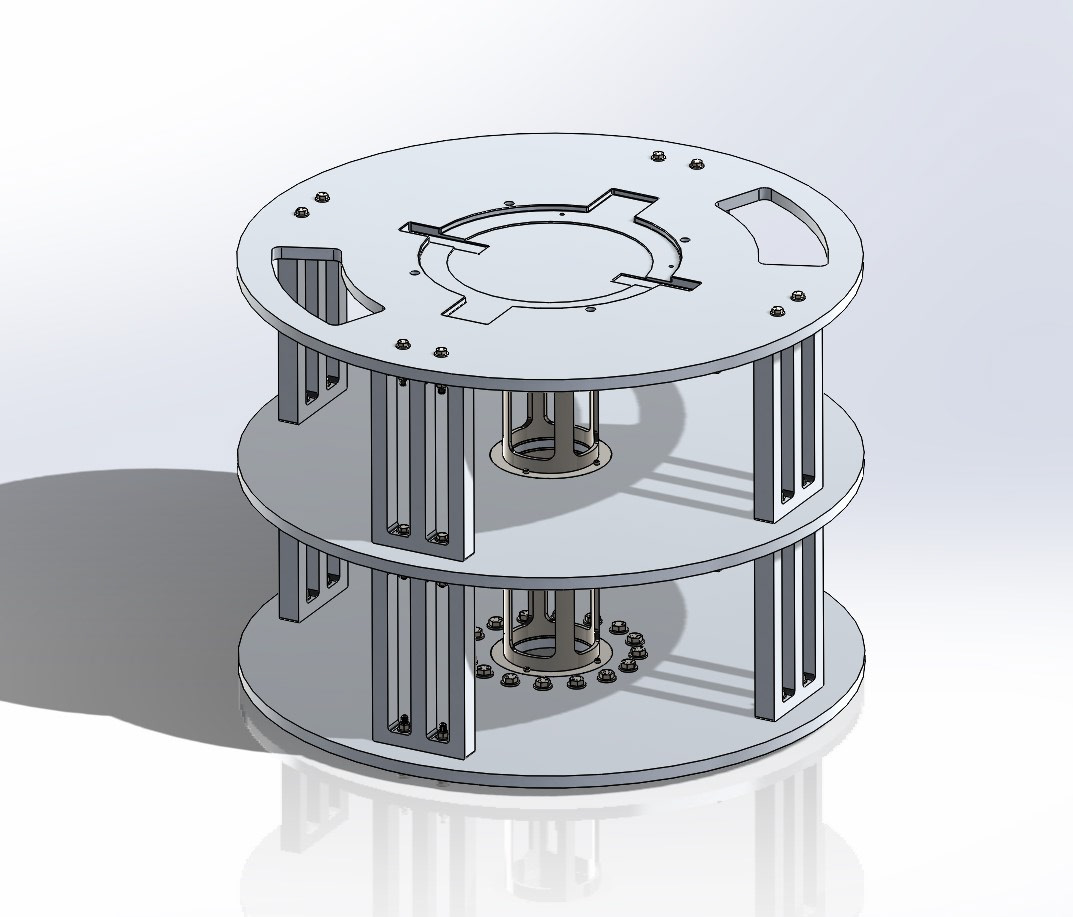
The next aspect of the device was the table. The main goal of the table is to hold computer and DAQ equipment that are mounted on the device. Due to the rotation of the tank, mounting computers directly to the rotating portion is the easiest solution. The angular velocity and acceleration are also relatively low so balance is not a major concern, but can be addressed by adding weight to the table. Initial tests were done with model hardware to try and determine configurations that were relatively balanced. Key features include a center channel to pass plumbing and wiring up from the rotary union at the bottom of the device, large top side cutouts for DAQ wiring and ease of assembly, and a modular design to use a one tier table if desired.
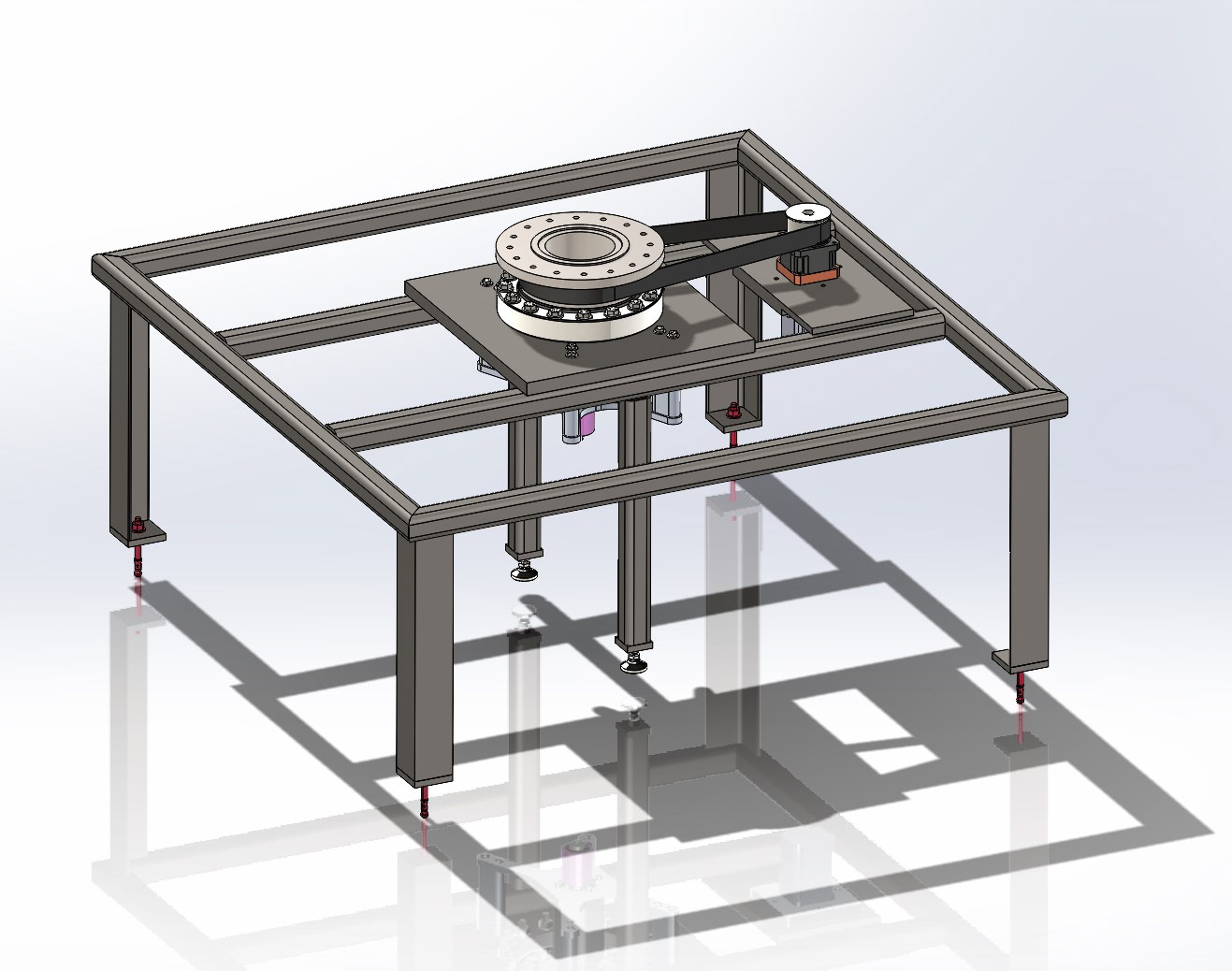
The last major subsystem of the design is the lab frame, which supports the entire device and measurement equipment. The frame is made from A36 structural steel and will be blasted and coated to resist the corrosive liquids used in experiments. The other job of the lab frame is to support the motor assembly, rotary union, and slip ring. Key features of the lab frame involve the integration of a MMC turntable. The large silver piece in the center of the table was developed to integrate the turntable and bottom table. Simulations were run to verify the strength of the frame and load bearing components. After simulation the center legs were added to the table with leveling feet to accommodate various table weights and the tubing wall thickness was modified for robustness and to reduce deflection. In the second design iteration the motor assembly is going to move to a more integrated solution so the majority of the table design will change.
This project was a great learning experience for me where I got to handle the complete design of a relatively complex assembly. Some areas that I would want to improve on are the interfaces between components, further simulation on the heat exchanger, and a reduction in hardware needed to assemble the device. As a first iteration I'm extremely happy with the design and the timeframe that I was able to finish the project in.