More detail on this project can be seen below but for those that want a quick overview here is a slide from the end of year design showcase:
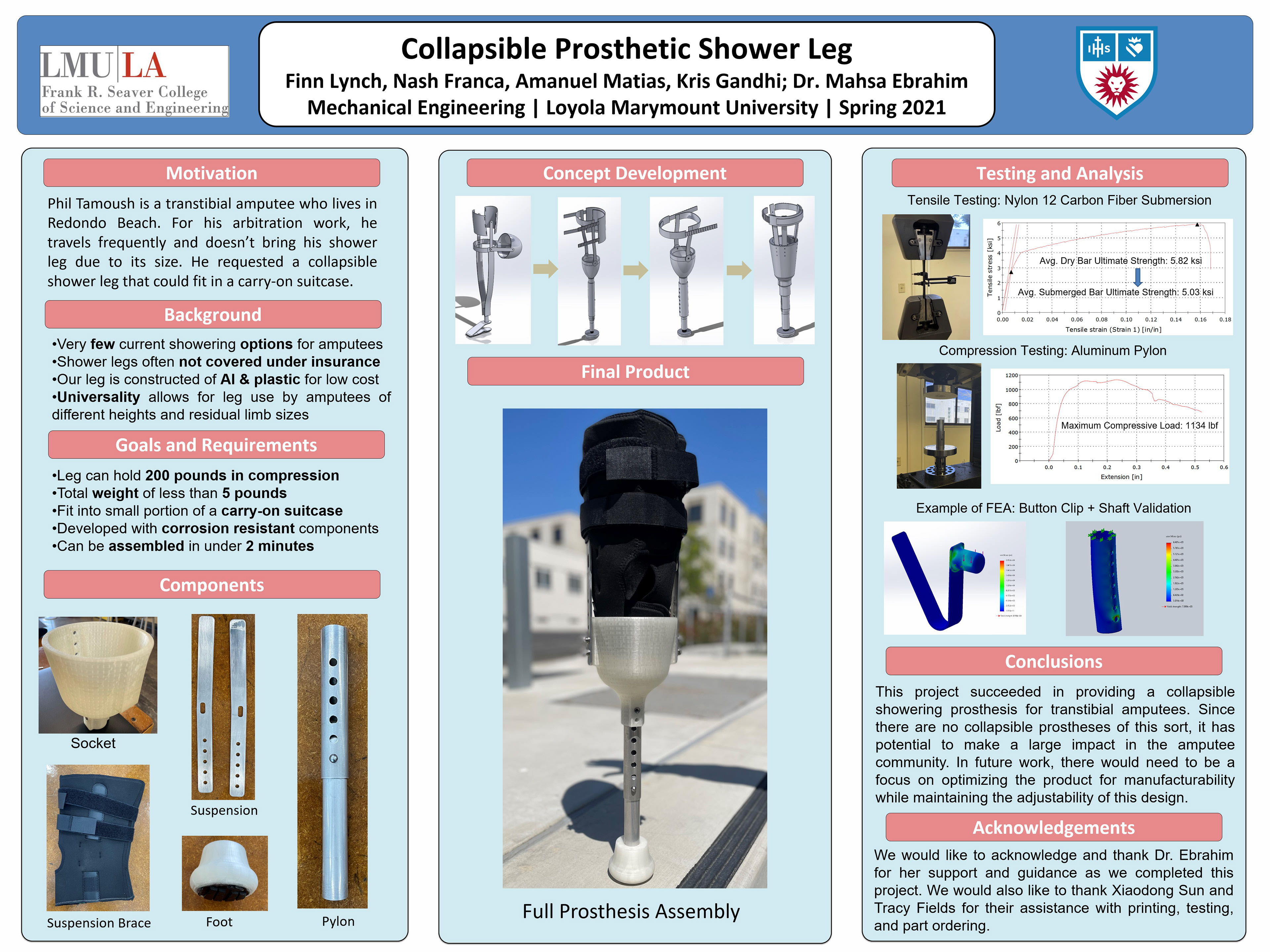
For my senior design project I worked on a team with three other seniors to design a collapsible prosthetic shower leg for an amputee in our community. We are working with a man named Phil who was looking for a prosthetic shower leg that he could use while traveling. The requirements we outlined were that the leg needs to be lightweight, have a small footprint, slip resistant, water resistant, be adjustable, and relatively low cost compared to a custom prosthesis. More detailed requirements can be seen below.
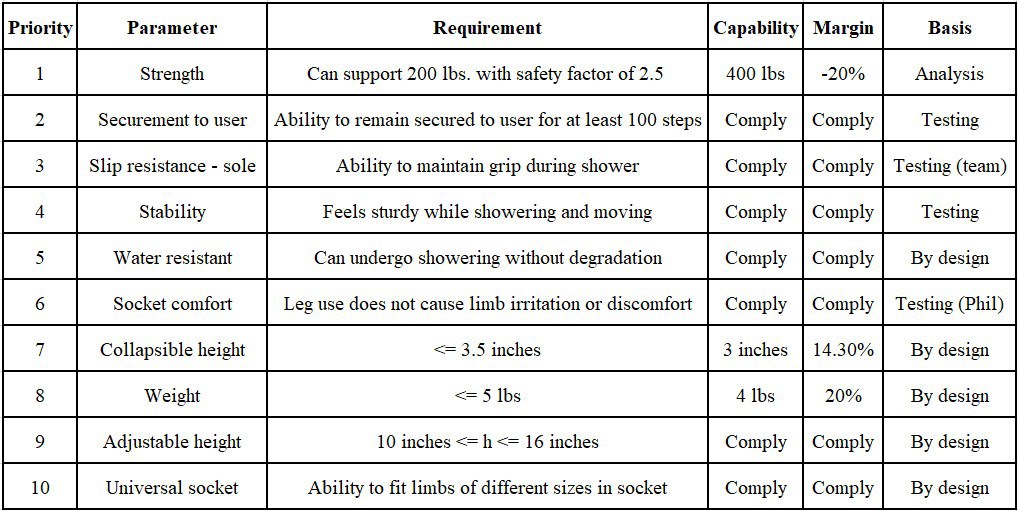
The four main components of the design are the suspension, socket, pylon, and foot. My primary responsibility was the design of the suspension and socket, and I also managed the CAD part and assembly files for the team. To start the design process we originally focused on the design of the suspension system. We knew that to achieve the collapsibility goals some telescoping leg would be needed. We also chose to use threads and spacers for fine adjustment and security of the foot.
The second design iteration focused more on the socket integration into the pylon. An idea to improve the integration was to use threaded inserts, but this made the socket bulkier than desired. The first two iterations are seen below with placeholder internal socket geometry.
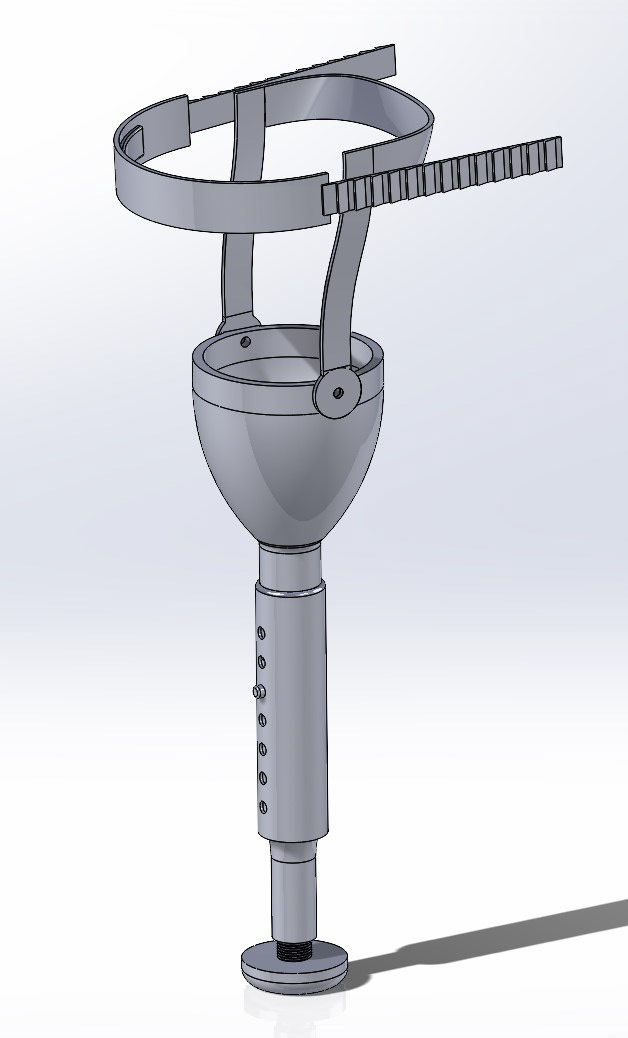
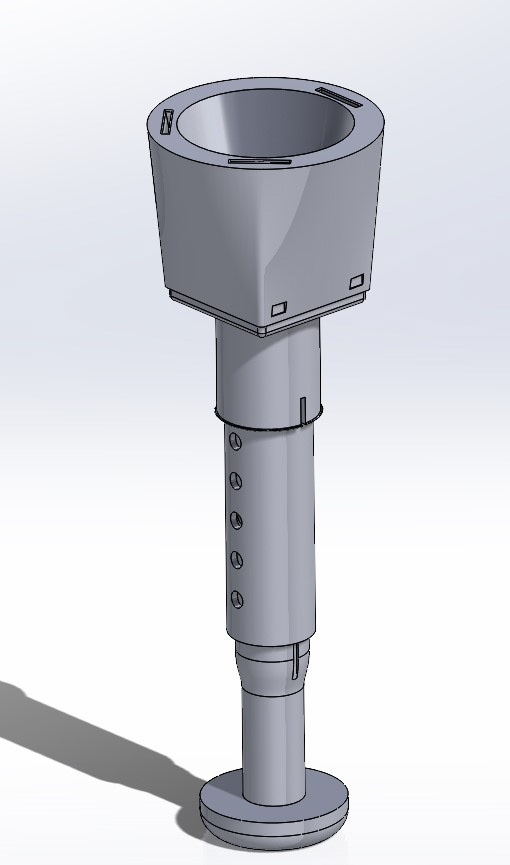
The next serious iteration moved away from the threaded inserts to a clamped interface. Using the clamp and a hollow socket the design exceeded our collapsibility goal and were completely tool-less which is ideal for travel. The next iteration and 3d printed sample are seen below along with the collapsed and extended views.

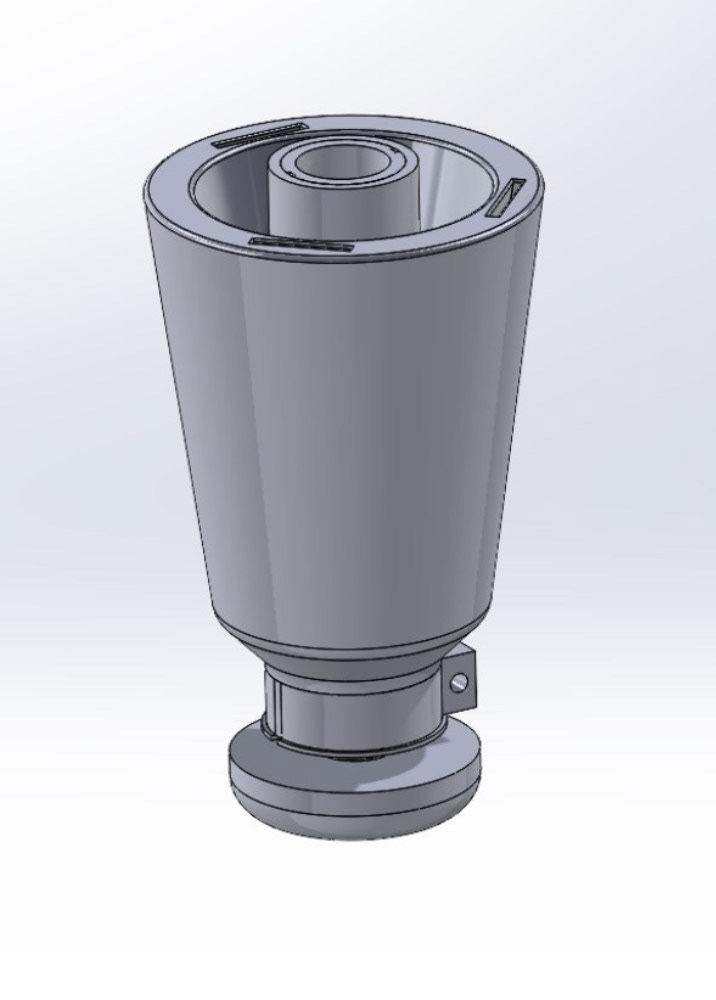
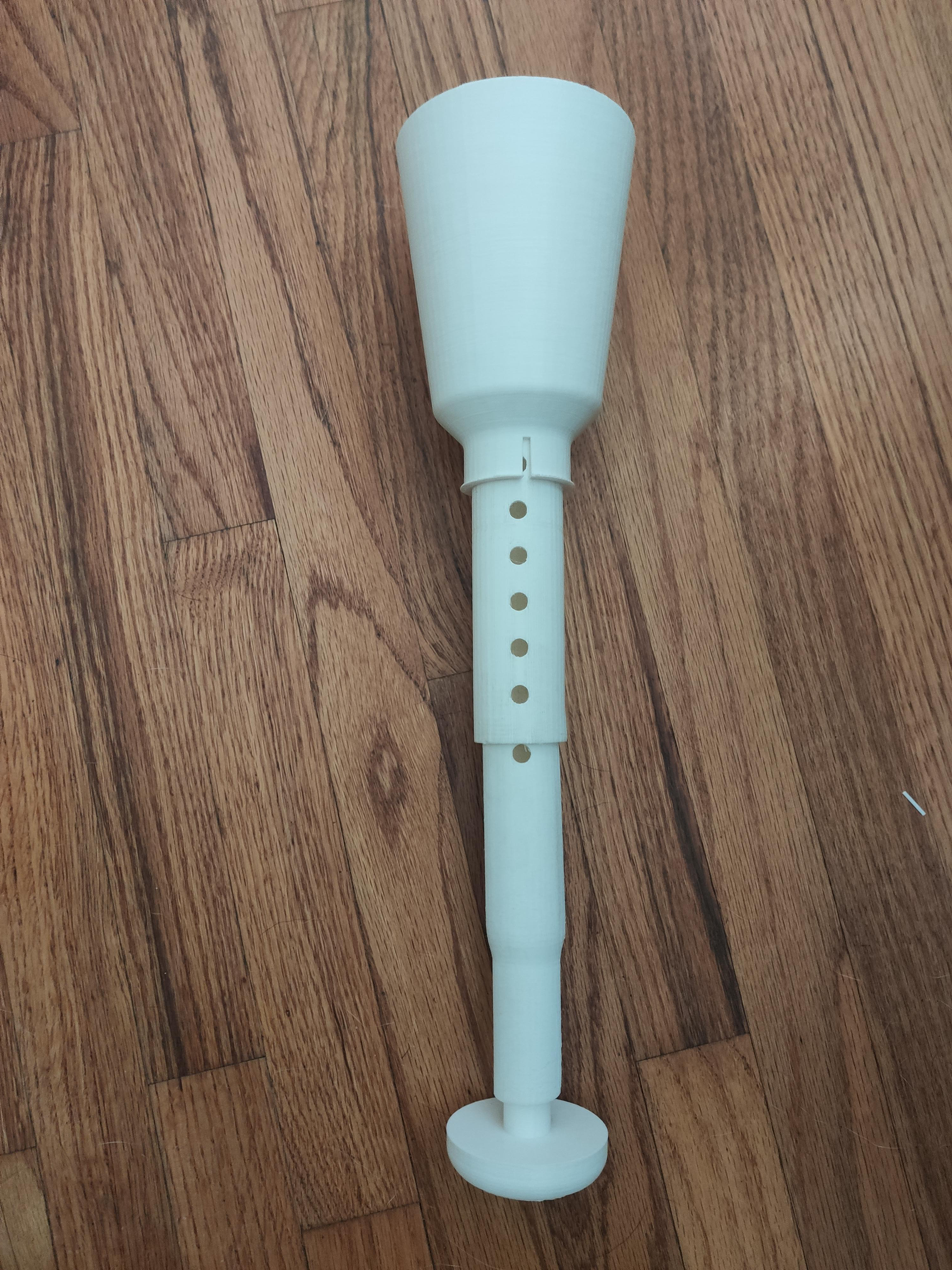
After some testing and further iteration on this prototype the final design strategy was determined. The main updates are a larger and more rounded socket. This allowed the residual limb to fit lower and be more confidence inspiring while walking. With the changes to the socket came changes to the supports. Rather than having multiple supports around the leg, two sturdier aluminum supports were used. A knee brace was then mounted to the supports to wrap around a larger portion of the leg which helped to better distribute the weight of the user compared to the single strap. The final design is seen below as the 3d printed prototype leg.
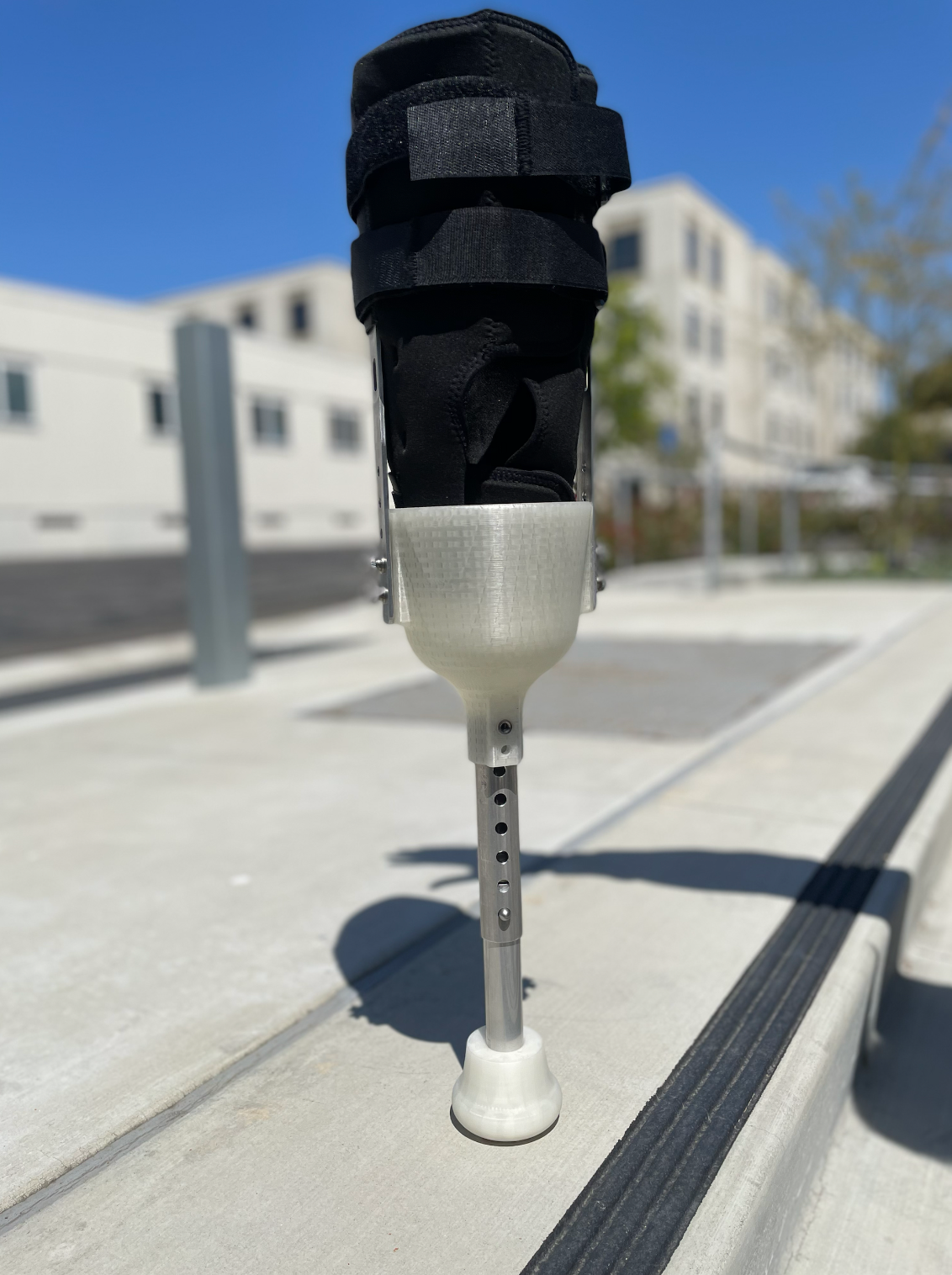
This design still has some flaws, mainly regarding stress concentrations and weak points in the brace. Analysis was performed on all parts of the leg and physical testing was performed on the pylon and interfaces major interfaces in the socket. The strength of the leg was found to be sufficient for Phil to do static standing tests (while being supported) such that he could give more realistic feedback on the comfort and ease of donning for the leg. Student will continue work on this project in the 21-22 school year and hopefully Phil will have the chance to try a more robust prototype.